GARMENT DYED
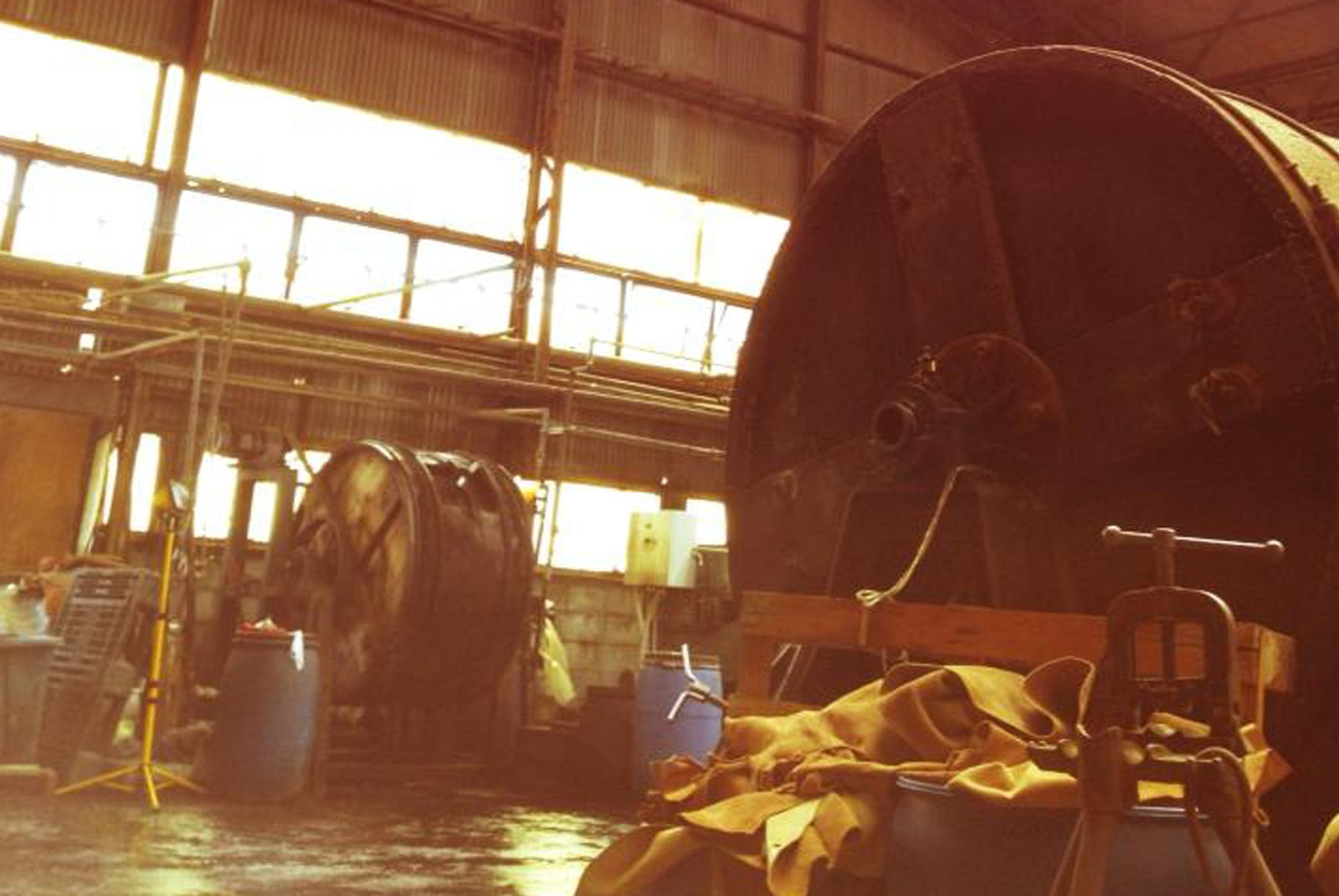
This is an introduction to "STRUM product dyeing".
Depending on the manufacturing process, leather has a big difference in the appearance and comfort of the finished product, as well as the appearance and discoloration of the atari.
STRUM leather is made with the idea that "the more you wear it, the more you wear it."
Please take a look at how the leather wear sold at STRUM OFFICIAL STORE is made.
1. Sewing in the state of the base
In order to achieve the ideal finish after dyeing, the leather is sewn into a rider's mold with the leather base adjusted and adjusted with oil. (The photo is the base of white tanning)
2. Dyeing
Just like when dyeing leather, it is dyed while rotating in a large wooden barrel called Tyco.
3. Drain and dry
Drain the dyed riders
Let it air dry over time while shaping each piece.
When it is about 80% dry, hang it on a hanger to further shape it.
By dyeing the product, it shrinks by 1 to 1 to 2 sizes. As a result, puckering occurs in the sewn part, and the ZIP that does not shrink creates a swelling, old-fashioned taste.
4. Lining correction and hand fir work, final finish
When it is completely dry, fix the lining and knead the hard, freshly dyed leather one by one by hand.
A few more steps are added to give the surface a luster, giving it a supple and soft finish.
Finally, fine-tune the size to complete.
In this way, STRUM leather wear goes through many processes and takes time and effort to finish each piece.
The real thrill of product dyeing is that the more you wear it, the more glossy and tasty it becomes, and the more you wear it, the more your facial expression changes.
The expression is completely different depending on the lifestyle of the wearer, and it is a leather jacket that grows into your own unique outfit.